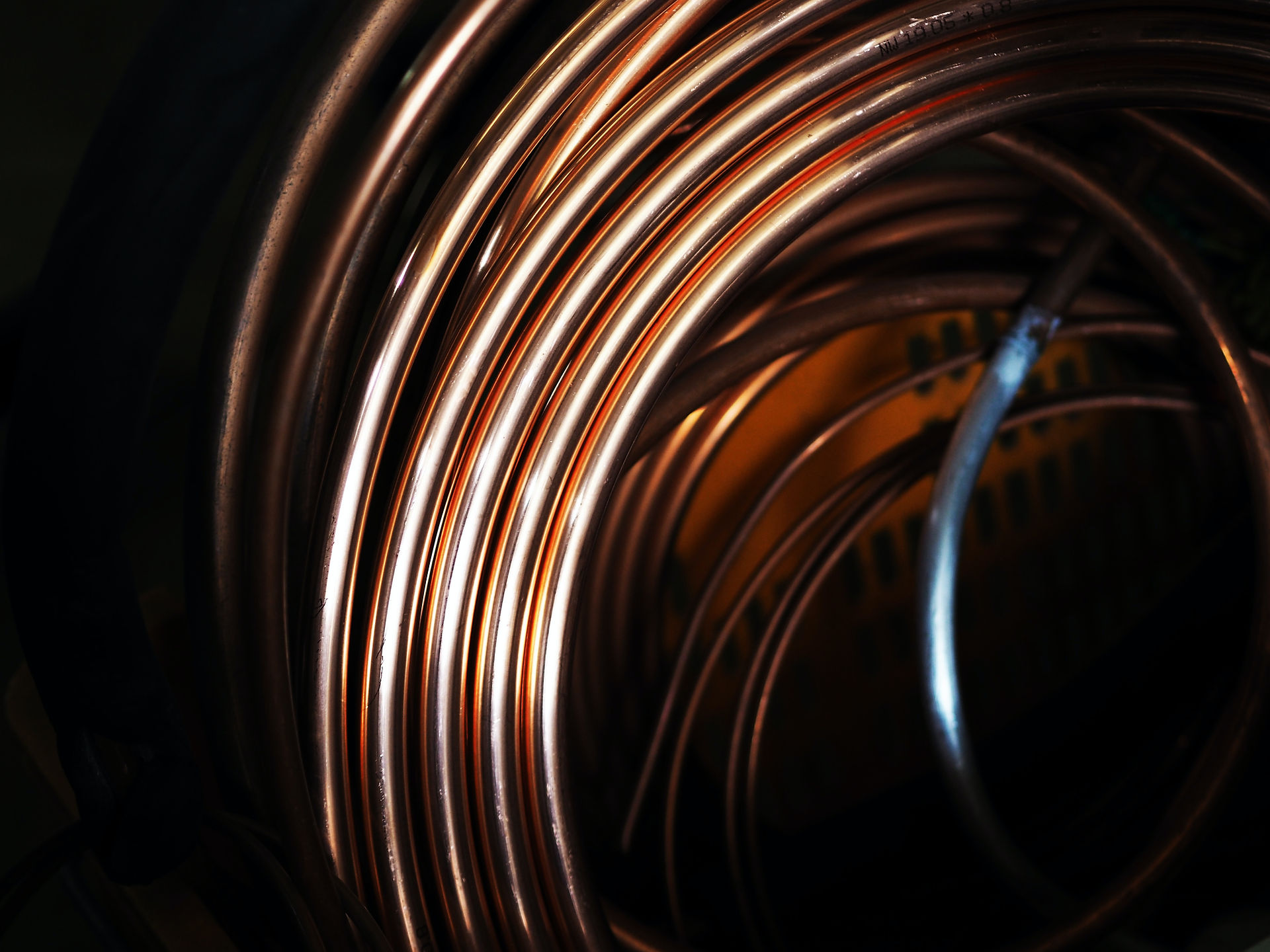
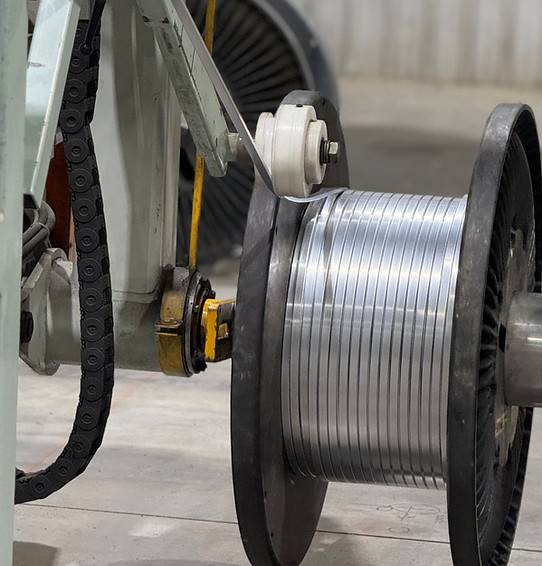
The Process - Continuous Rotary Extrusion
The United Kingdom Atomic Energy Authority (UKAEA) invented the continuous extrusion system in 1971 whilst looking for a method of producing seamless tubes for the storage of spent nuclear fuel rods.
The process, was ultimately not used for that application, but other commercial possibilities became apparent and over the past 50+ years, the process has been developed and used for a variety of products.
​
​
Continuous Rotary Extrusion (CRE).
It is used for the continuous production of both aluminium and copper extrusions.
​​​
​​​
​​
​​
​​
​​
​​
​​
The process utilizes a rotating grooved steel wheel, approximately one-quarter of which is enclosed by fixed sealing segments to form an extrusion chamber. An abutment extends into this chamber, effectively obstructing the groove in the wheel.
These sealing segments are integrated into an extrusion shoe, which is securely held in place within the extrusion machine by high-strength clamps engineered to withstand the significant pressures generated during extrusion.
​
Aluminium or Copper feedstock, typically in the form of rod, is introduced into the groove at the entrance of the extrusion chamber. As the wheel rotates, the material is carried forward until it encounters the stationary abutment. The resulting interaction generates substantial frictional heat and pressure, raising the temperature of the metal until it reaches the plastic state. Under continued rotational pressure, the softened material is extruded through a die, completing the extrusion process.
The animation on the left was generated using QForm UK, a specialized software platform offering advanced, scientifically validated simulation tools to support research and development in metal forming technologies.
​​
​​
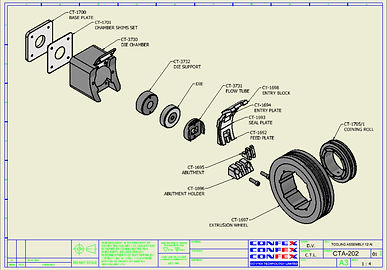